高品質・短納期のフルモールド鋳造
『Casting X』とは
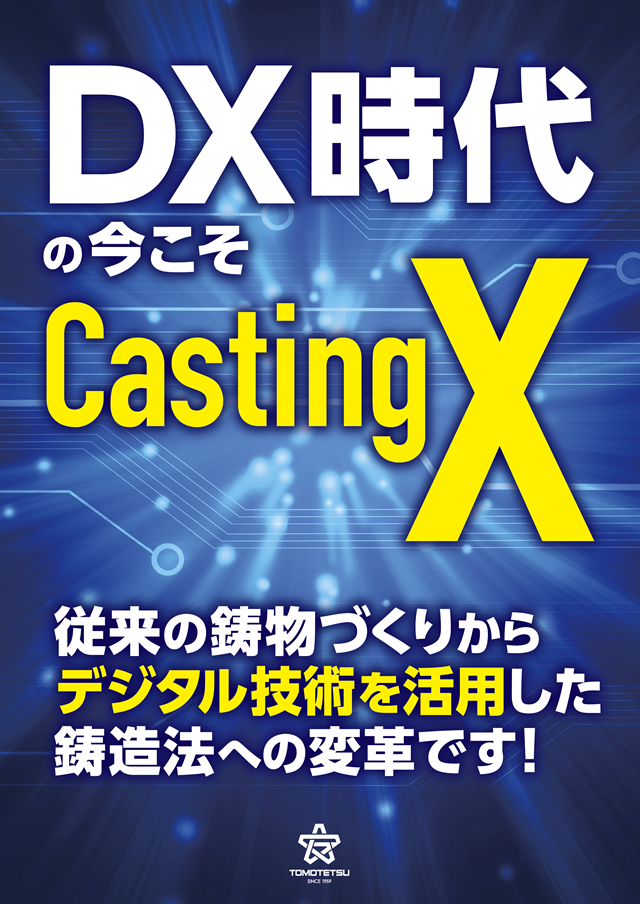
友鉄工業株式会社では、自動車部品製造(鉄板プレス・アルミダイカスト)向けの金型用鋳鉄素材を製造(社内製造比率70%)しており国内自動車メーカー及び部品メーカーへ納入しています。
又、海外でも使われています。
その中で、自動車の開発リードタイムはどんどん短くなっており、我社ではお客様から金型データを受け取ってから3週間で、鋳物素材を納入しています。
これら自動車の開発スピードへの対応で培ってきた3Dものづくりの技術を活かして、自動車業界以外の産業へのお役立ちを提案していきたいと考えています。
そこで、DX時代の今こそ『Casting X』を導入され、従来の鋳物づくりから「デジタル技術を活用」した鋳造法への変革を提案したいと思います。
プロセスとしては、
- 3Dデータを頂く(2Dしかない場合は3Dに変換します。)
- 3DCAD/CAMシステム8台と24h稼働のNC加工機4台で発泡スチロール模型を(分割加工・組立)製作します。
- 3Dレーザー測定器で寸法検査を行います。
- 消失模型(フルモールド)鋳造法にて、木型レスで鋳物素材を製造します。(月産850t)
- 3Dデータは加工工程に活用できます。
- 3Dスキャナーによるリバースエンジニアリングも可能
特徴としては、
- 単品の大型製品(2t~10t)で、短納期(3~4週間)を達成
- コストダウン(30~50%)が実現可能
- 試作段階におけるフレキシブルな修正(発泡スチロール模型での修正容易)
- 3Dデータを活用したスムーズな一貫加工
- 「木型レス」なので模型の保管が不要
- 模型データ保管による素早いリピート対応
品質 :
木型に比べバリも無く、高精度での鋳造が可能
木型を用いる場合、上型と下型の組合せによって鋳造を行う為、多くの場合「バリ」が発生してしまいます。
バリが発生することで「バリ取り」等の二次工程が必要となり品質、納期、コスト面にも影響します。
フルモールド鋳造は、発泡スチロールで製品と同形状の発泡模型を作り、その発泡模型を砂型に埋め溶湯との置換によって製品を創りだします。これによりバリが発生し難く、複雑且つ高精度な製品を創り出す事が可能となります。
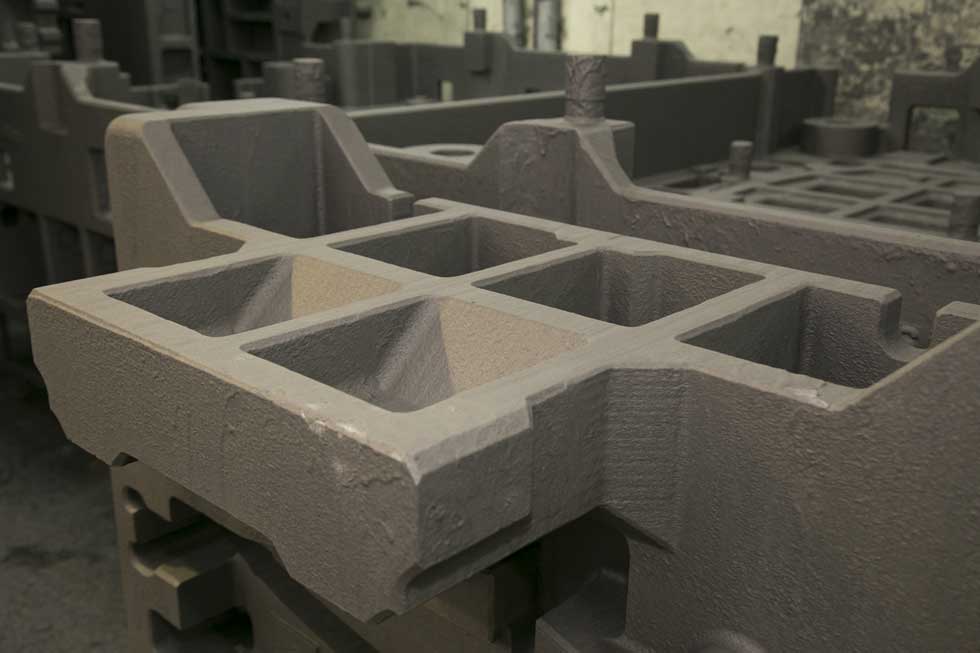
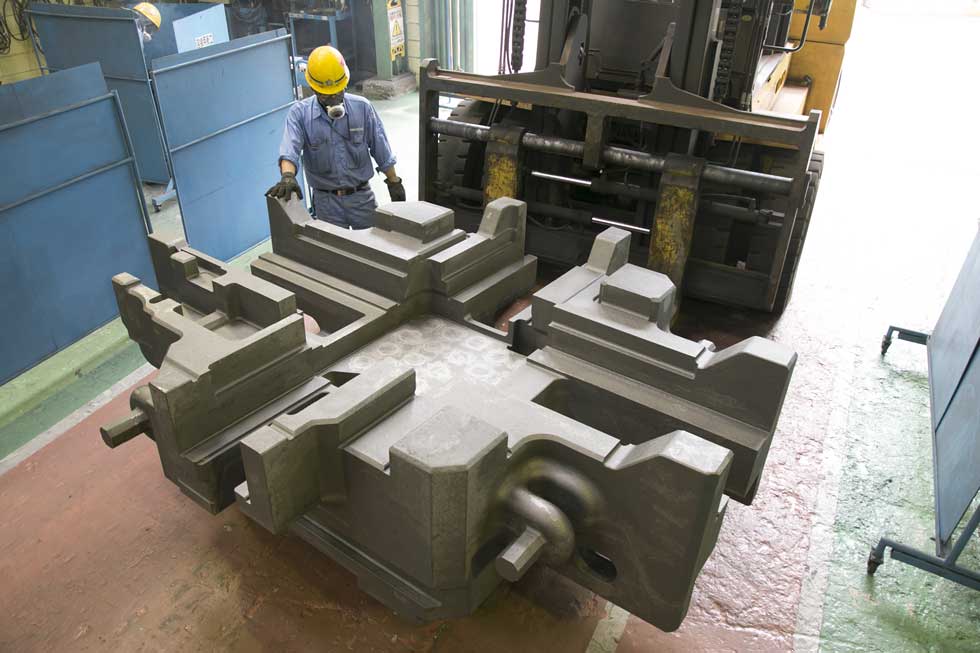
コスト :
複雑形状でも3DCADによるモデリングで工程数も少なくコストメリットが高い
従来の木型による鋳造は熟練技術が必要となり、特に複雑な形状は厳しい鋳造条件や、中子・抜け勾配などの鋳造方案により自由度が制限され、納期・コスト面で課題がありました。
フルモールド鋳造法の場合、複雑形状であっても複数のパーツに加工した発泡スチロールを組み合わせる事で発泡模型を製作することが可能です。
当社では、3DCADを用いてモデリングを行い、マシニング加工で発泡パーツを作り、発泡模型を製作します。従来の木型に比べ製作期間、コスト面においても非常に有利となる上、木型保管の必要もなく、劣化によるメンテナンスも不要な為、現在幅広く用いられる鋳造法です。
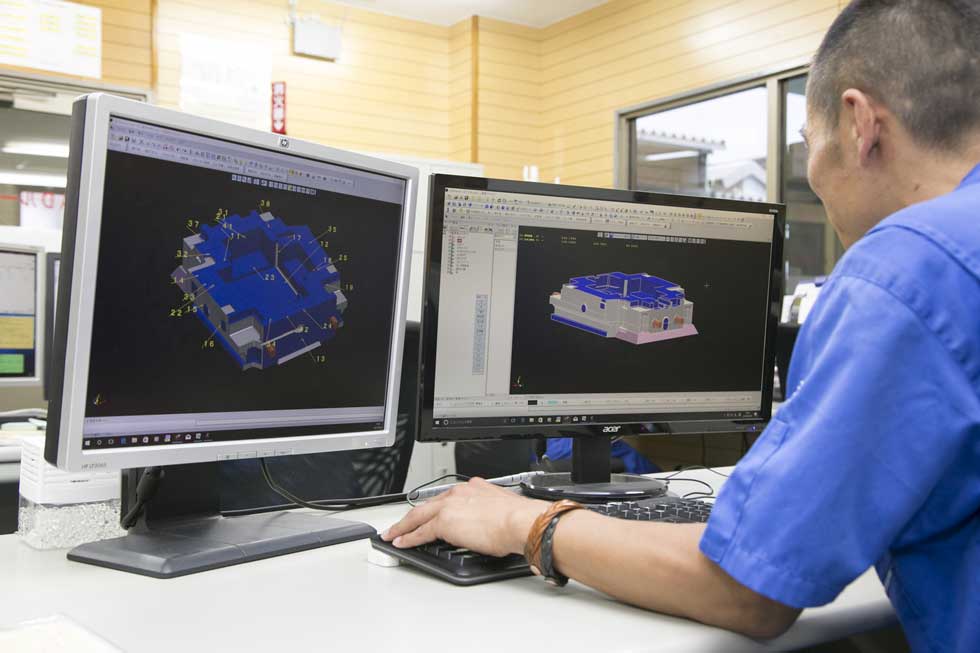
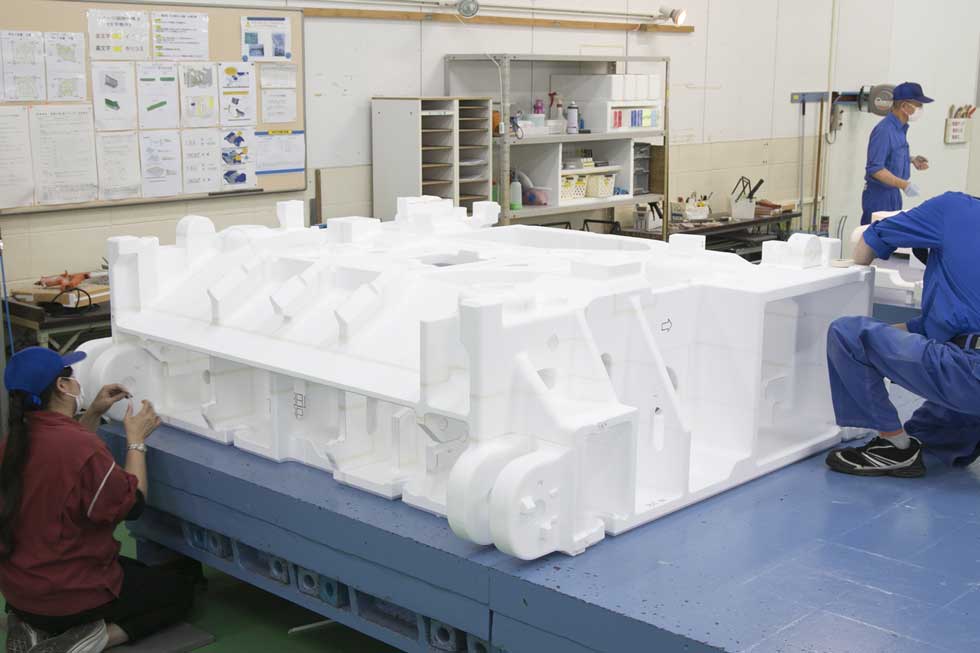
納期 :
木型の鋳造に比べ工程数が少なく、設計変更が容易
フルモールド鋳造は木型に比べ、工程数が少なく納期が早いのが特徴です。
また発泡模型段階で製品形状の確認ができるので高品質化を図るとともに、急な仕様変更や設計変更にも柔軟に対応でき、設計上の問題も事前検証することが可能です。
それは結果として、設計から鋳造までのリードタイムを短縮し、製作期間の短縮を図ることが可能となります。
更に当社では、CADCAM設計者を常時10名配置し、モデリングからマシニング加工、組み立て、検査など、社内で一環した模型製作を行うことで、迅速で安心なお客様対応を目指しております。
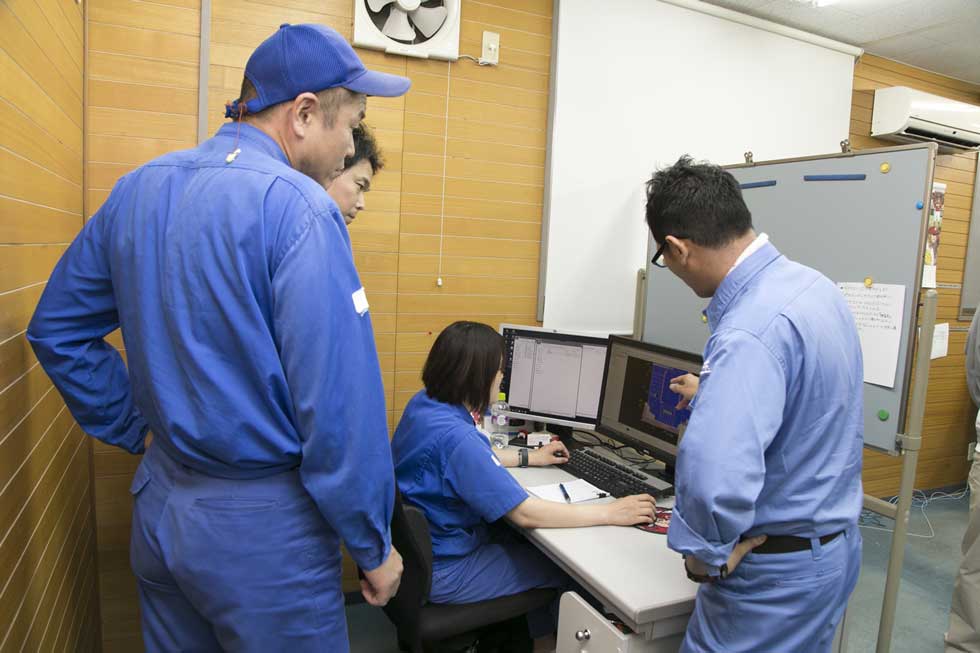
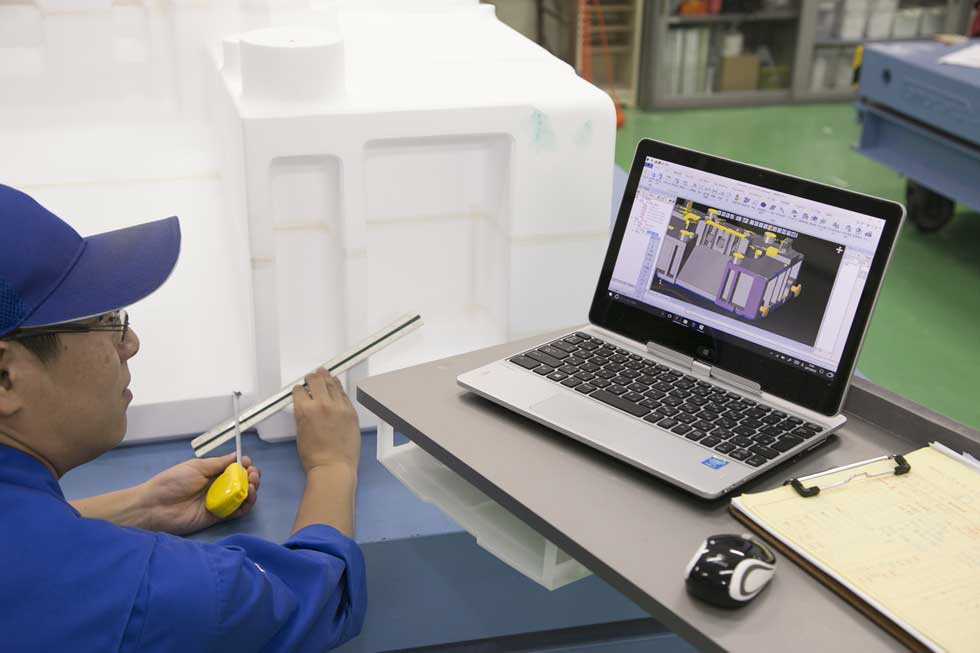
技能検定取得者
製品の品質向上、技能向上を目的に技能検定にチャレンジしています
鋳造技能士1級:39人 | 鋳造技能士2級:17人 | 溶解技能士1級:8人 |
溶解技能士2級:7人 | 鉄工技能士2級:1人 | 機械系保全2級:4人 |
機械加工3級:1人 |